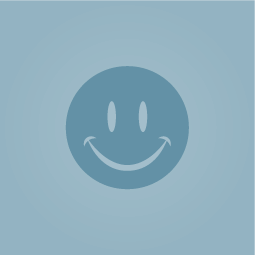
Romanian R&D Institute for Gas Turbines COMOTI
Looking for Partnership Looking for Extra EU Funds
The main activity of the laboratory is research &development in the composite materials area, targeting especially the aeronautic field applications. Understanding of composite materials and their structures requires a thorough knowledge of basic materials, their precursors. Knowledge about the behavior reinforcement (long, short, continuous, discontinuous fibers, particles, etc.) and matrices (thermoplastic, thermosetting resins, ceramic, etc.) is essential for understanding the complexity of manufacturing processes. The development, the study of composite materials, the manufacturing of laminates / parts / structures from composites using autoclave technology, currently considered as the most performing and the structural / mechanical characterization of composite materials through laboratory tests, using INCDT COMOTI infrastructure and equipment’s, are the main activities of the composite material laboratory.
The laboratory is able to accomplish and provide a complete technological cycle of manufacturing for laminates / parts from composites starting from design of laminates/parts and also of the moulds, selection of materials (composites, cores for structures, metallic insertions, etc.); structural / mechanical characterization of composite materials; manufacturing of molds in collaboration with Technology Research COMOTI department, manufacturing of composite laminates/parts using autoclave technology; laboratory testing (mechanical testing in static and dynamic structural tests, microscopy, etc.).
EQUIPMENTS
Autoclave for composite materials polymerization (SCHOLZ/2010)
-
Main characteristics: Temperature max. 400°C; Pressure bari; vacuum
-
Usable diameter: 1500 mm; usable length: 2500 mm; Load Agent: hot air
-
Operation: 400V/50Hz 3/PE
-
Control: 230V/50Hz/24V DC
-
Equipment Power: approximately 314 kW
-
Circular water consumption: 32,5 m³ / h at 32 ° C max
-
Water flow pressure: min. 3 bar, max 6bar
-
Air control equipment: 8-10 bar pressure
-
The incoming compressed air in the autoclave: max. 40 bars
-
Pressure: 0-20 bar
-
Speed variation / increase in temperature (20 ° C -400 ° C): ° C / min
-
Speed variation / decrease in temperature (400 ° C-65 ° C): ° C / min
-
Charging / charge maximum 20 kg composite; 100kg aluminum 350 kg steel (chariot)
Cold room
- Temperature: -18 °C
- Dimensions: 1200x1200x2000mm,
- Switchboard that allows setting the temperature and permanent view of the work temperature
Composite materials laboratory testing (using physics and mechanic testing laboratory facilities):
Universal mechanical testing machine: Instron 8802
- Force cell: 250kN; 25kN
- Strain Measurement with extensometers, strain gauge data acquisition system, LVDT for displacement measurements
- Hydraulic grip
- Tensile, compression, bending devices
- Furnace (temperature max. 1000°C) used for high temperature metallic materials testing)
- Software BlueHill and WaveMatrix (Instron)
- Materials: Steel, Plastics, Composite, Wood, textile materials
Static regime:
- Tensile
- Compression
- Bending
Dynamic regime:
- Fatigue: Low Cycle Fatigue and High Cycle Fatigue (LCF and HCF)
- Fracture mechanics: KIC (plain strain fracture toughness), CTOD; (crack tip opening displacement), J integral, etc.
High Resolution Scanning Electron Microscope FEI Inspect F50 (Field Emission Gun)
- Resolution: 1,2 nm; acceleration voltage: max. 30 KV
- Microstructural high resolution investigations on: metals, ceramics, glasses, polymers, geological samples, etc.
- Nanomaterials, thin films observations, fracture surfaces examination
- X-ray spectrometry (EDS annalyses): identification and quantitative evaluation of chemical elements in samples, on structural elements: precipitates, inclusions, etc., evaluation of compositional gradients.
Olympus optical microscope GX ()
- Usual microstructural analyses on metallographic samples
- Identification of metallographic phases and constituents
- Quantitative evaluation of structural elements
Impact/ drop weight impact machine Dynatup 9250NV Instron
- Power cell with self-identification of the total weight of the sleeper, including additional weights, maximum speed of falling: from to m/s
- Maximum speed at assisted fall by the hair bows: 18 to 22 m/s
- Speed accuracy: ±
- Maximum height of fall: 1200 - 1300 mm
- Sleeper positioning accuracy ± mm (or % of reading)
- The position repeatability: ± mm
- Energy impact: to 945 J (with additional weights)
- Speed of movement of the sleeper to reactivate test: 1550 to 1650 mm/min
- E nvironmental, climatic chamber with an operating range of -60°C to 200°C
Keywords and matching areas:
Get Access to the 1st Network for European Cooperation
Log In
or
Create an account
to see this content
Intelligent Energy
Renewable Energy
Industrial Engineering
6 years ago
Please Log In to See This Section